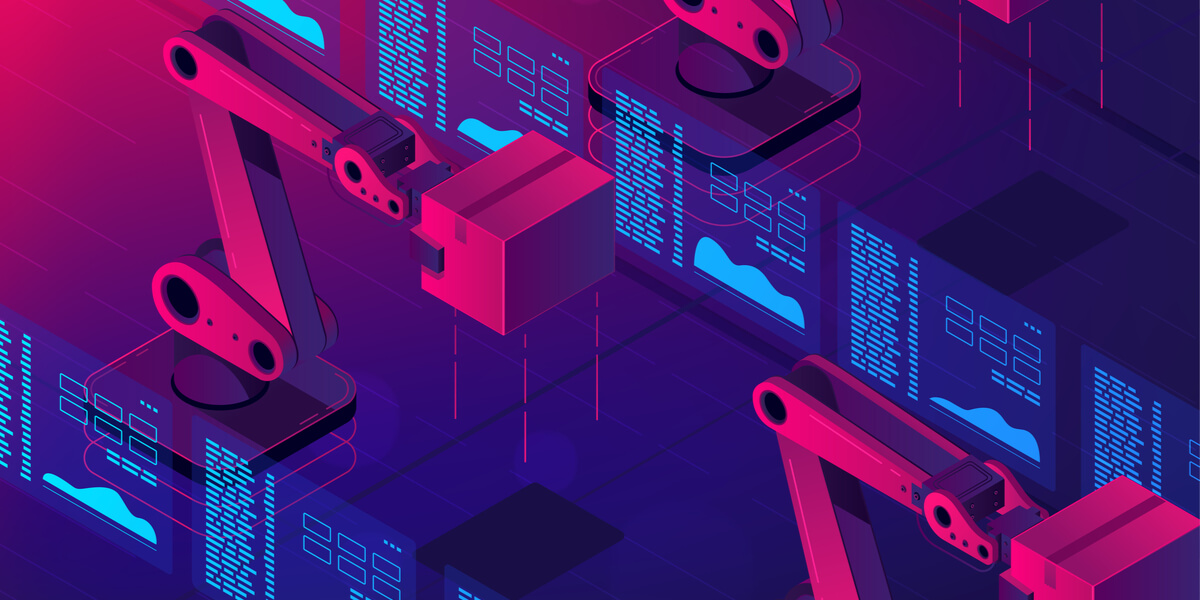
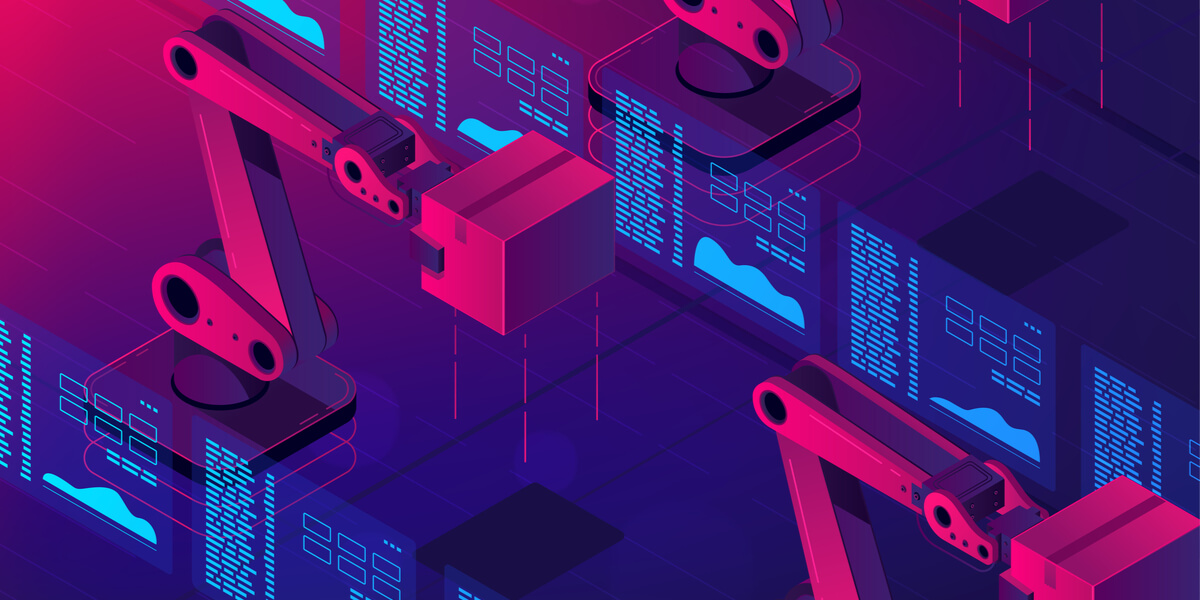
As companies redesign workplace safety protocols post-COVID, manufacturers will have to make some of the most significant changes. One of those changes will be how workers interact with the Workforce Activities Module in Kronos.
Many manufacturers use Kronos Workforce Activities module because it’s proven to be one of the most precise tools to track manufacturing's direct versus indirect labor hours.
Activities can give managers immediate insight into productivity, order status, grant usage, scheduling, productivity, and absenteeism. It also automates and reconciles any labor allocation when an employee works multiple jobs (a tracking necessity for manufacturers!).
With real-time insight, it’s easier to track efficiency and make changes before it dings your bottom line. This will be especially critical if a production facility opens with partial staff.
Activity & Labor Tracking
For instance, if a meat processing plant has a sales order from a retailer, the employee enters that job tracking number into Kronos Activities using a clock or kiosk. That shift fulfills the order, and when it's finished, the employee closes the job order. A worker, or a team of workers, may have a dozen job orders or more to enter (and close) at the clock on each shift.
In a Post-COVID workplace touching the clock dozens of times a day to enter data could put employees at risk.
According to Improv Senior Application Consultant Chuck Sodos, the touch requirement for those using Activities is different than punching the time clock or biometric clock upon arriving to work.
“Companies using Activities to track each job order use the clock extensively, so designing a way to keep people safe will be a priority as workers return to plants,” says Sodos.
For many manufacturers, revising Activities use will be in addition to redesigning workstations, installing dividers, and extending assembly lines.
A WFM Balancing Act
“Manufacturers who have remained open, at least partially, have been figuring these things out along the way but a lot of plants are really going to be challenged to balance safety and productivity as they restart or rollout operations,” says Chuck.
5 Manufacturer Tips
Chuck offers these tips for manufacturers using Kronos:
-
Provide workers with a tool such as gloves, a finger cot, or special rubber-ended pen that allows them to safely engage with the clock.
-
Periodically clean clock surface with a glass cleaner applied to a soft, lint-free cloth. Never apply a cleaning product, solvent, sanitizing gel, or wipe directly to the clock — it could ruin your device..
-
Secure Job Packs (orders/job instructions) by handing them off in plastic sleeves and wearing gloves to minimize contact.
-
Post signs reminding employees to wear masks on the job and other appropriate Personal Protective Equipment (PPE). Read more on PPE time tracking here.
-
Get daily updates on manufacturing-specific issues such as stock room and loading dock safety, workstation reallocation, equipment and tool safety, and social distancing best practices via OSHA’s daily newsfeed.
The Good News
Companies using Activities will have a production edge because the feature allows shift supervisors to view the status of every work order or production operation underway. This increases the supervisor’s ability to recognize and respond to delays or issues created by process changes.
“As manufacturers gear up, it’s going to be important to have the ability to create and track all labor tasks and subtasks and measure hourly productivity to make up for the months of closures,” says Chuck. “Using Activities, companies can make solid commitments to their customers, which will help everyone bounce back."
Are you a manufacturer redeploying your workforce? Do you need help configuring your Kronos Activities? Improv can help. Let’s talk today.
Meanwhile, if you're looking for ways to build better schedules in Kronos post-COVID, download our recent webinar and grab yourself some new skills!
Comments